In simple terms about Aestech frameless glazing technology: redefining the future of architecture
Aestech engineers have developed a method of frameless glazing using new-generation insulated glass units. It allows you to build truly transparent and warm transparent facades, terraces, and atriums.
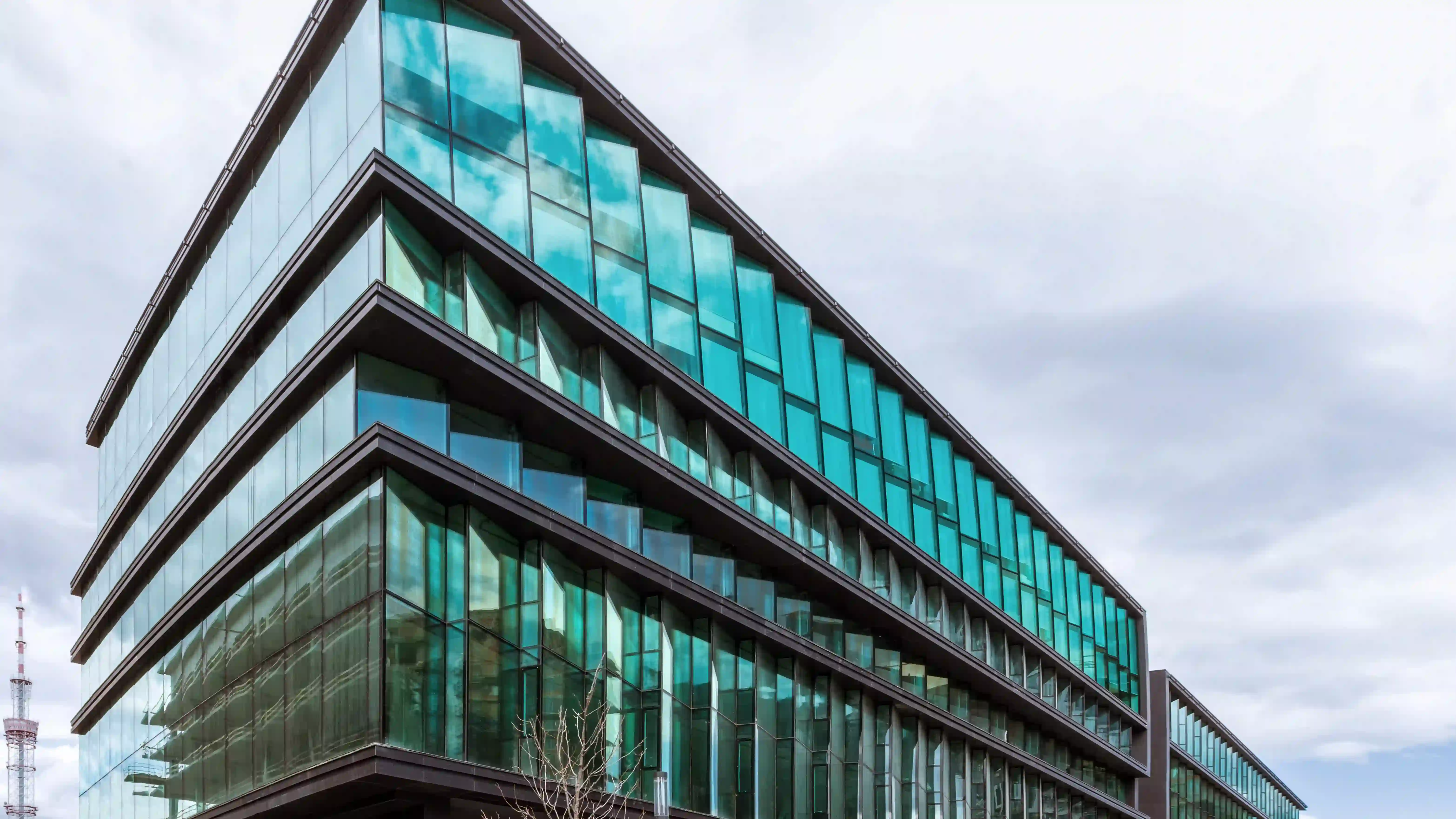
Aestech News
It is difficult to imagine a modern work of architecture without large glass facades, atriums, and terraces. It is the latter ones that distinguish buildings from typical urban "boxes" and give them a futuristic look. But let’s take a closer look. Oddly enough, you will see that most glass structures are not all glass.
Designers' and architects' dreams of a "one-piece glass wall" are usually shattered by safety requirements. And the requirements are strict: first of all, the glass facade must withstand the battle with the main enemies — wind and precipitation, to the extent clearly defined by building regulations. Esthetics goes by the wayside. And now, a translucent project, beautiful on paper, turns into a web of metal racks, crossbars, frames, and spiders in reality.
Is it possible to get rid of the metal frame in the glass facade? Not with standard solutions. But over 10 years ago, Aestech engineers discovered an unconventional one. Thanks to the new technology, dozens of buildings with strong and beautiful glass facades, transparent terraces, and roofs appeared. What is important — they are energy efficient.
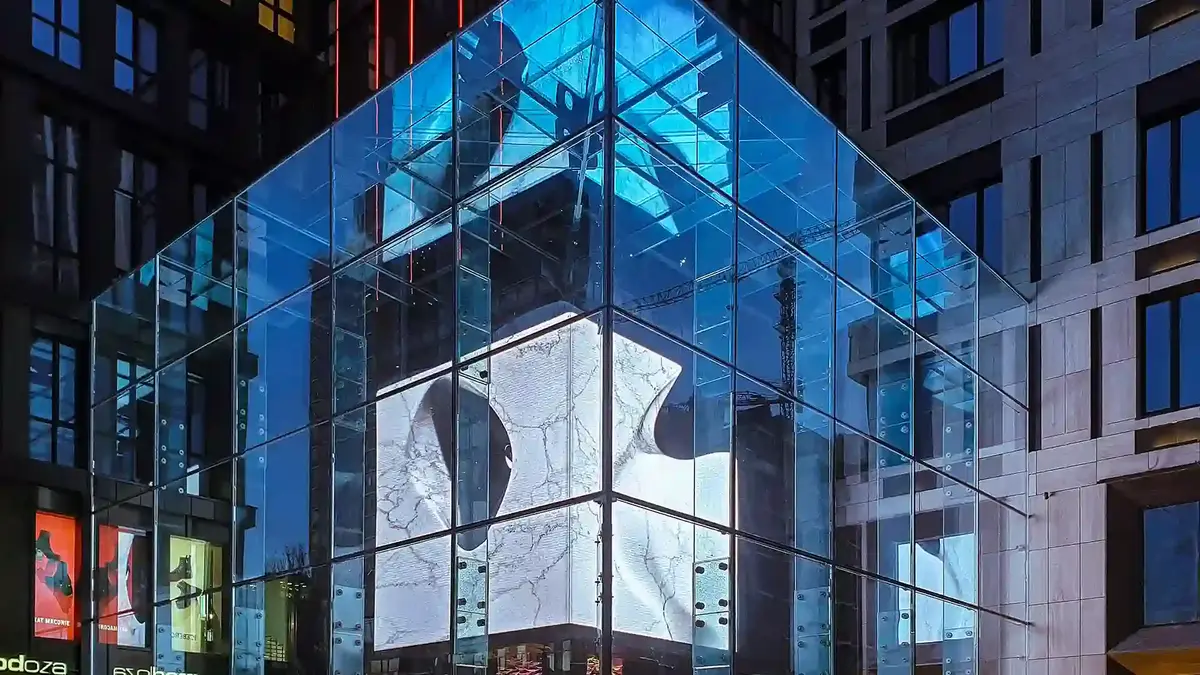
What a standard insulated glass unit can and cannot do
Why is it that we need to use so much auxiliary metal for glazing? To figure this out, let's look inside a standard glass unit.
Typically you will see two or three layers of glass separated with a metal spacer and held together by a secondary sealant. Glass forms chambers protecting the premises from noise and outside weather.
We remember: the main task of a translucent enclosing structure is to protect the premises from wind and precipitation and to remain intact. This is where difficulties begin with a standard glass unit. Fundamental one — in the method of connecting glass layers.
The secondary sealant used for bonding is quite soft. This means that the double-glazed unit is not really a monolithic system, as it seems, because during loads, the glass layers hardly interact with each other. For example, if the wind blows, more than 90% of the load goes to the outer glass only. Internal ones "rest" from this work.
It turns out that the outer glass must be made thicker with each level of height, so that the wind does not bend or break it. However, the price of glass increases non-linearly with every millimeter of thickness. It is expensive to produce, transport, and install glass. Therefore, the size of double-glazed windows usually has to be limited to 3 x 1.1 m. But even then, standard insulated glass units have to be reinforced. Double-glazed windows are pressed against the frames, aluminum racks, and crossbars, spiders as a support, to take part of the load from the glass.
Therefore, it is impossible to make reliable glass facades without supporting structures. You can’t ignore the laws of physics. But how is it possible to transfer the external support inside the glass unit itself? This is exactly the vector that Aestech developers took.
How to make an insulated glass unit a self-supporting one
In order to make the inner layers of the glass also resist the wind, it is necessary to rigidly connect the entire insulating glass unit system. Instead of a conventional sealant, you need a different, strong material that can withstand heavy loads, expand and contract under the influence of temperature changes like glass, so that the double-glazed window does not deform over time.
Aestech engineers did many experiments. Pultrusion proved to be the best. It is formed as follows: many glass threads are twisted into one large "rope", impregnated with resin, passed through a temperature chamber, and strongly stretched. At the output, a very rigid consistency is formed, with which the developers reinforce the glass unit along the entire contour. Everything is connected together with a special super strong glue.
This way, the double-glazed unit was transformed from several almost independent layers of glass into a single flat pipe. And it’s a completely different physics. The "pipe" is able to withstand ten times more load than a standard insulated glass unit, due to the fact that the glasses transmit forces to each other.
A double-glazed window made according to this scheme is called "insulated glass unit with higher stiffness", or IGUHS. Its main advantages over conventional double-glazed windows are self-sustainability and lower weight. Say a developer wants to install a 4.25 m2 window that can withstand a wind load of 60 kg/m2. A standard insulated glass unit with such characteristics has a weight of 234 kg, IGUHS — almost half as much — 126 kg.
The most important thing is that with such stiffness characteristics, the new generation insulated glass unit does not need external supports. That is why Aestech's technology opens up new horizons for designers of glass structures, which they never even dreamed of until recently.
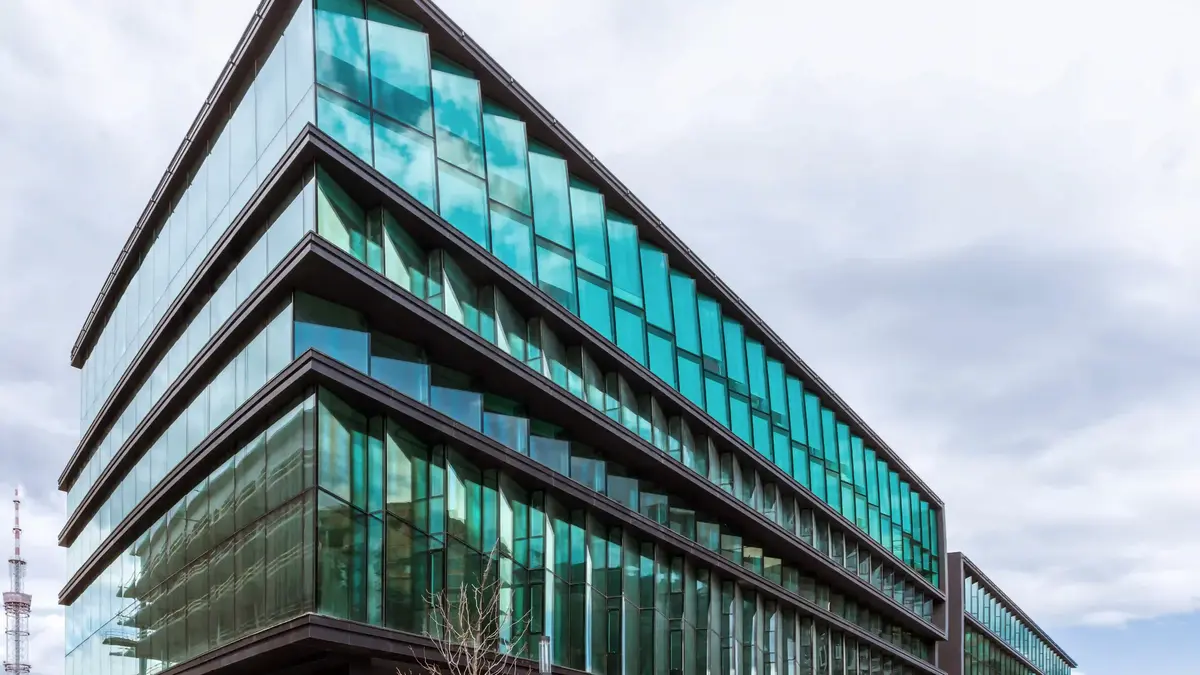
Here are just a few architectural and development tasks that our know-how solves.
1. Higher energy efficiency.
The metal used in standard glazing technology heats and cools more than glass, forming cold joints. These are additional costs for cooling the premises in summer and heating in winter. We remove it thanks to IGUHS — and the whole structure becomes more energy efficient.
In addition, pultrusion is very close to glass in its coefficient of linear expansion. Thanks to this, the glass unit reacts evenly to temperature changes and remains airtight. Another advantage is that the coefficient of thermal conductivity of pultrusion is the same as that of wood.
Finally, the problem of gaps disappears, because there are no racks and crossbars. Insulated glass units with increased stiffness can be mounted end-to-end with each other, closing thin seams with sealant and gaskets.
2. Large dimensions.
IGUHS can be made large, several times larger than the standard one. The size is limited only by the possibilities of production of high-quality large-format glass. For example, we have successfully implemented projects with insulated glass units of 6 x 3.21 m — it is like the area of a large room.
3. Easier transportation and installation.
We have already said that an insulated glass unit with increased stiffness is much lighter than a standard one of the same size. This makes its transportation easier and cheaper.
In addition, the fasteners of the double-glazed window can be screwed directly into the pultrusion, and the entire structure can be connected directly to the load-bearing parts of the building. Also, unlike standard technologies, with IGUHS you can start glazing as soon as the first floor is ready.
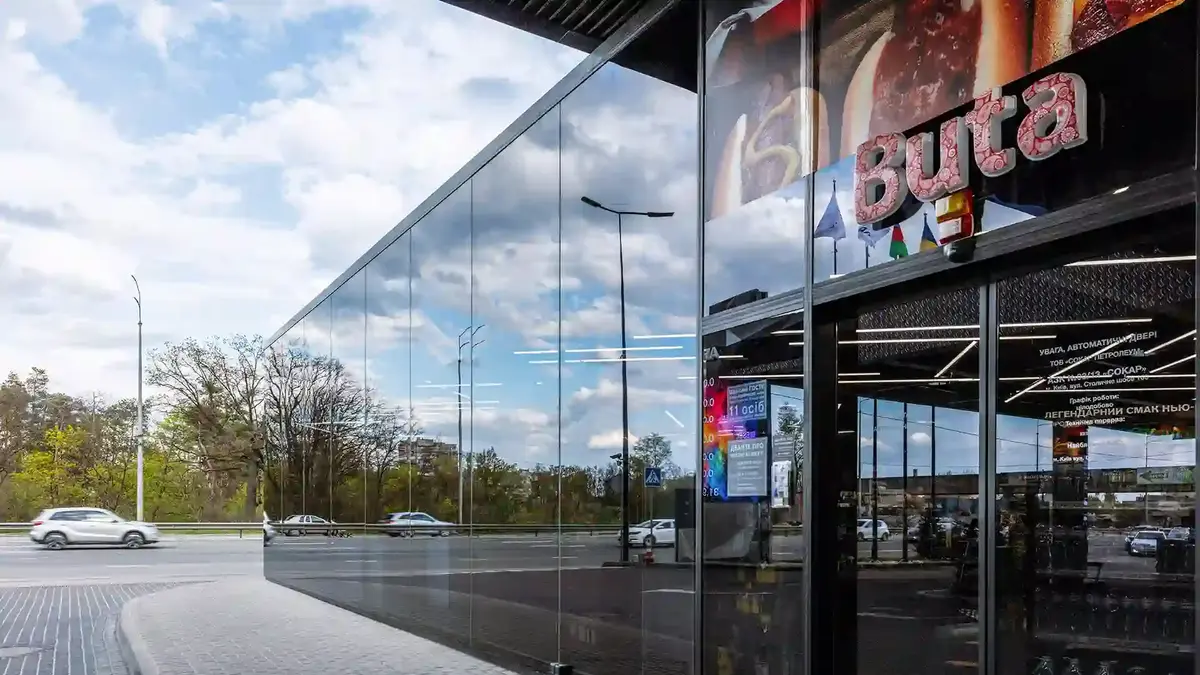
4. Even reflection.
If you look at large windows and facades in hot or cold weather, you will see that every single glass unit has a distortion. This happens because the gas inside the chamber expands or contracts due to temperature changes — and thus puts pressure on the outer glass.
You won't see this in IGUHS. Due to the rigid construction, the changes in gas volume in the chamber cause the glasses to stretch each other rather than bend separately from each other. But glass reacts very little to stretching. Therefore, a terrace or facade made of IGUHS gives an even reflection, which is what its architects intended.
5. Aluminum factor.
Our glazing technology overcomes the complete dependence on aluminum in construction. When removing metal from a facade or terrace, you:
- do not contribute to the pollution of nature, since the production of aluminum is very energy-consuming and "well-known" for harmful emissions;
- do not spend money on the purchase, delivery, processing, and installation of profiles;
- speed up the installation of a facade or terrace;
- save on utility bills, as a facade without metal is much more energy efficient;
- improve the external and internal appearance of the building, as well as free up additional squares inside that could be occupied by supporting frames.
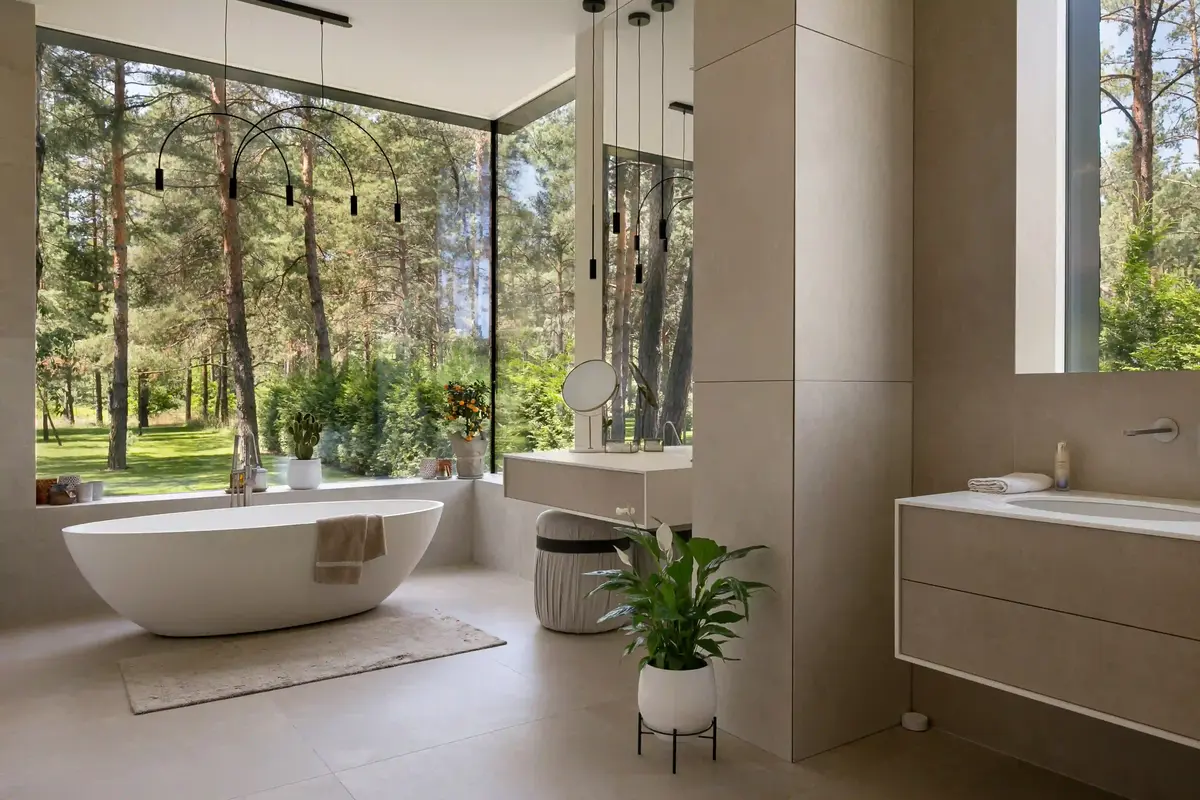
These are the main but not complete features of our frameless glazing technology. We continue to develop and work so that the EEE formula — that is, "ergonomics-energy efficiency-esthetics" — becomes the standard of modern architecture.
Contact us, and we will be happy to help you realize your dream project!